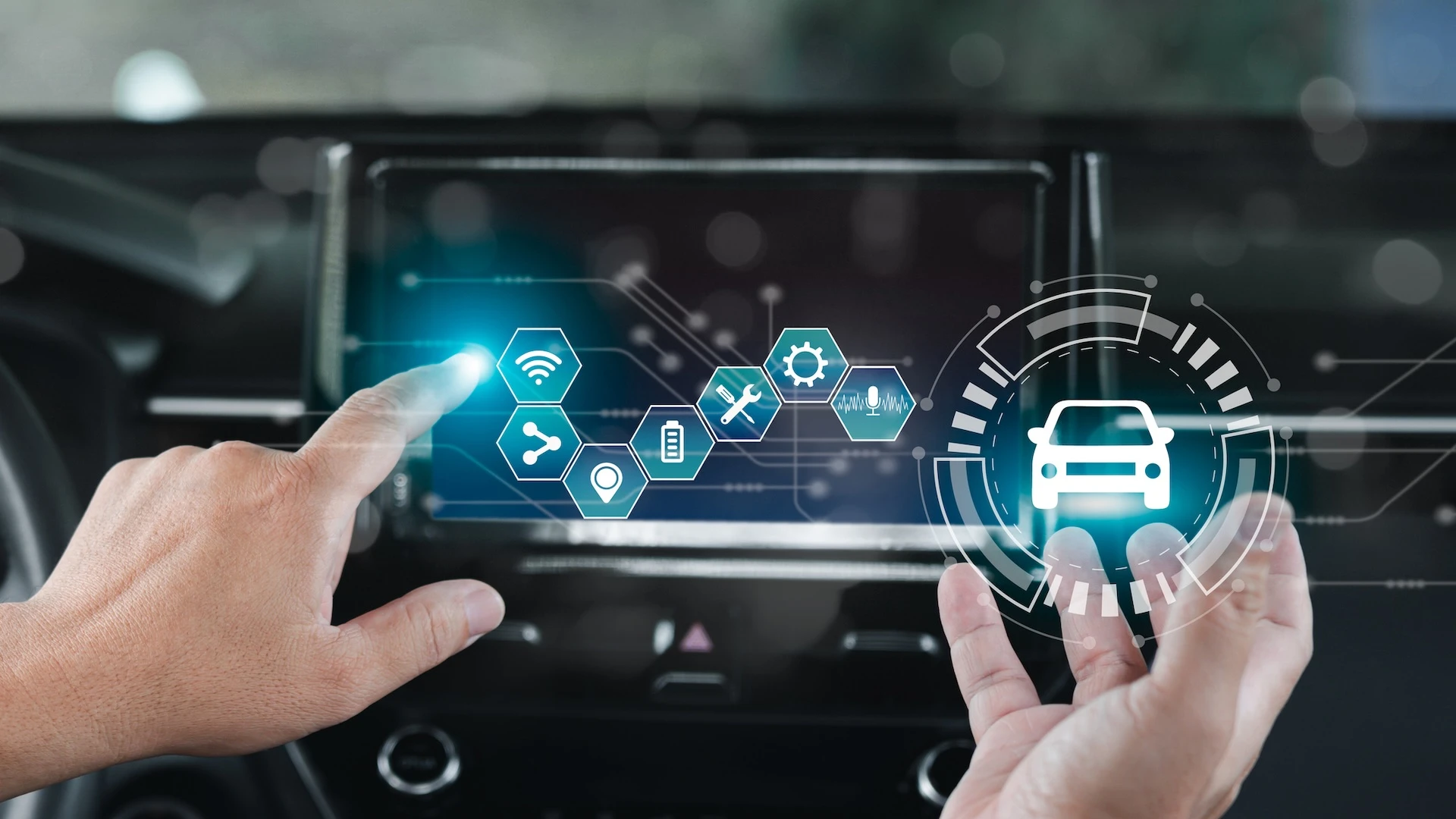
Let’s be honest—our throwaway culture isn’t working. Mountains of discarded parts, wasted resources, and unnecessary costs. But what if we could flip the script? The circular economy isn’t just a buzzword; it’s a game-changer for industries drowning in spare parts they don’t know how to handle. Here’s how reusing and refurbishing can turn waste into worth.
Why Reuse and Refurbish? The Bigger Picture
Think of spare parts like puzzle pieces. Toss one away, and suddenly, the whole picture’s incomplete. Refurbishing keeps those pieces in play—saving money, slashing waste, and cutting carbon footprints. It’s not just eco-friendly; it’s wallet-friendly.
The Environmental Payoff
Manufacturing new parts guzzles energy and raw materials. Refurbishing? It can reduce CO2 emissions by up to 85% compared to making replacements from scratch. That’s like swapping a gas-guzzler for a bicycle.
The Business Case
For companies, it’s a no-brainer. Refurbished parts often cost 30-50% less than new ones. And with supply chain hiccups becoming the norm, reusing what you’ve got is a buffer against delays.
Key Strategies for Spare Parts Circularity
1. Implement a Take-Back Program
Ever seen a coffee pod recycling scheme? Same idea, but for industrial parts. Encourage customers to return used components—offer discounts or loyalty points as incentives. It’s like a library system, but for machinery.
2. Standardize Parts for Easier Refurbishment
Not all parts are created equal. Designing components with modularity in mind—think LEGO blocks—makes disassembly and reuse a breeze. No more wrestling with proprietary screws or glued-together monstrosities.
3. Build a Robust Inspection Process
Refurbishing isn’t about slapping a new coat of paint on a rusty gear. Rigorous testing—like ultrasonic scans or stress tests—ensures parts meet original specs. Otherwise, you’re just passing along problems.
4. Leverage Digital Twins for Tracking
Digital twins—virtual replicas of physical parts—let you track a component’s entire lifecycle. Know when it was last serviced, how many cycles it’s endured, and when it’s due for refurbishment. It’s like a medical record, but for machinery.
5. Partner with Local Refurbishers
Small workshops often have the expertise (and flexibility) to breathe new life into niche parts. Collaborating with them builds regional resilience—less shipping, faster turnarounds, and community job creation.
Real-World Success Stories
Enough theory. Here’s who’s nailing it:
- Caterpillar’s Reman Program: Their refurbished engines perform like new but cost 40% less. They’ve processed over 2 million components since 1973.
- Philips’ Medical Equipment: By refurbishing MRI and ultrasound machines, they’ve cut costs for hospitals by up to 60%.
- Apple’s Robot Disassembly (Daisy): It recovers rare materials from iPhones at a rate of 200 units per hour. Not perfect, but a leap forward.
Common Roadblocks (and How to Dodge Them)
“Refurbished” Stigma
Some still equate “used” with “inferior.” Combat this with transparency—show certifications, testing data, and warranties. A 12-month guarantee speaks louder than marketing fluff.
Logistical Headaches
Reverse logistics—getting parts back—can be messy. Solution? Designate collection hubs or partner with third-party logistics providers who specialize in returns.
Regulatory Gray Areas
Laws around refurbished goods vary wildly. In the EU, WEEE Directive compliance is non-negotiable. In other regions? Do your homework—or risk fines.
The Future: Where Next for Circular Spare Parts?
Imagine a world where every bolt, bearing, or circuit board has multiple lives. With AI-driven quality checks, blockchain for part histories, and 3D printing to repair worn components, we’re closer than you’d think. The question isn’t “Can we afford to do this?”—it’s “Can we afford not to?”